An asphalt paving installation must be done according to the recommended preparation procedures. This type of asphalt pavement is long-lasting and resistant to the effects of weather and time. If proper pre-work is not done, asphalt pavement is likely to develop cracks, potholes, and other structural problems that warrant expensive repairs and, before their time, deterioration.
Site prep: clearing and grading
This stage includes the removal of the site and leveling it before paving. It involves the removal of vegetation, junk, and road obstacles to the concrete paving. In the sequential layers of materials, the clean and smooth surface will be the last thing left.
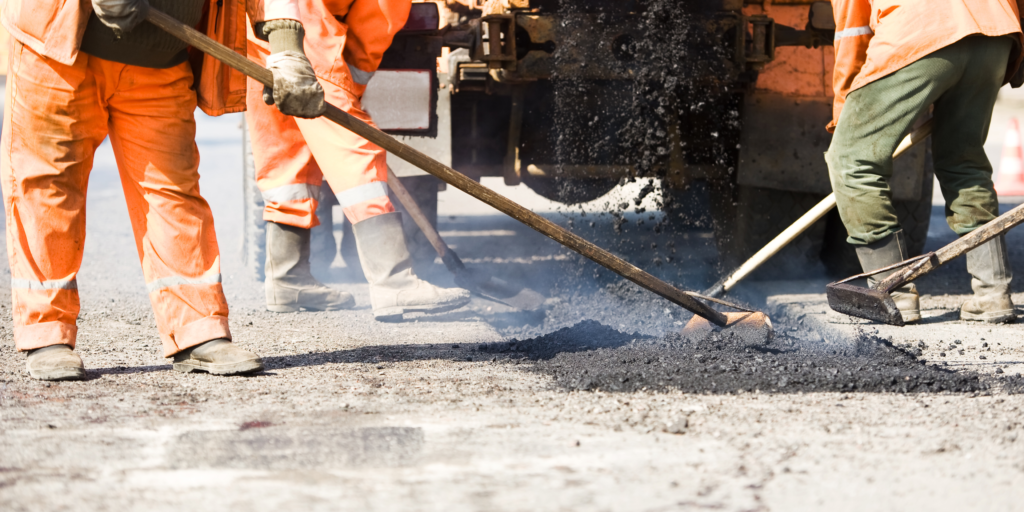
Trees, shrubs, and grass are generally the first components of site preparation to be removed. Trees growing on the streets cannot establish their roots under the pavement and, therefore, cannot cause harm. When cleaning the workspace, debris and lost things are cleared out.
Grading is used when cleaning the ground to establish drainage slopes and levelness. Earth grading functions to improve water drainage and prevent water loss. The lack of a drainage system can result in water infiltration, which can damage the pavement’s structure.
Inspection of Subgrade
Subgrade inspection is a mandatory factor for proper preparation of asphalt paving. As a result of asphalt going on the subgrade, which is the dirt or pavement underneath it, the pavement will be very smooth. The test must be undertaken to reveal any defects that could result in problems with the asphalt pavement’s performance.
To determine its structural integrity, the subgrade is inspected by visual examination, soil testing, and geotechnical analysis. Manual inspection targets areas of softness or too much water. Soil testing is an analytical procedure that allows for the identification of composition content, compacting, and load-bearing capacity.
Geotechnical analysis involves a series of tests on the soil carried out in the field and the laboratory to determine the engineering features. The experiment shows the subgrade’s stability, amount of moisture, and how supportable the asphalt pavement is.
Installation of Base Material
The correct base material is essential for the durability and quality of asphalt pavement. A durable base material distributes stress evenly and prevents the asphalt from cracking or sinking under heavy traffic.
Road pavement is composed of aggregate and crushed stones, as well as recycled materials. The base material’s differences depend on the volume of traffic, climate, and budget.
Installation causes the base material to be densified and stabilized by the compaction process. Rollers or compactors, heavy equipment, are used to compact the foundation layer. Adequate soil compaction is the most effective way to stop pavement settling and distortion.
Drainage Considerations
If drainage is not properly addressed, asphalt paving may face significant challenges. Water can lay on the surface if there is no proper drainage system, resulting in early degradation and damage to the structure. An adequate drainage system needs to be planned and implemented considering the life of the pavement.
The installation of asphalt pavement is a process that considers water drainage problems. The grade influences how water drains off the pavement. The slope should work to direct the water to the catch basins or storm drains.
Designing and Testing Asphalt Mix
It is essential to have the asphalt mix with the proper design and testing, as it is crucial for the pavement to be of high quality and perform well. Asphalt mix design is about choosing the best aggregates, bitumen, and additives to have all the desirable properties, such as flexibility, durability, and resistance to cracking.
The traffic volume, climate, and the level of pavement use are considered when designing and testing asphalt mixes. High-traffic roadways may require a different proportion of the aggregate in their mix design than the one for the residential streets.
When evaluating asphalt mixture performance, mix design is performed, as in laboratory studies. These tests identify the optimum binder contents, rutting and fatigue cracking resistance, and moisture susceptibility.
Mix design and testing give paving specialists an opportunity to test asphalt pavements for compliance and durability.
Equipment and Staff Needed
Asphalt paving installation is machinery and labor-intensive and hence demands the correct equipment and labor. The project size, complexity, and available resources primarily determine the size and type of the equipment.
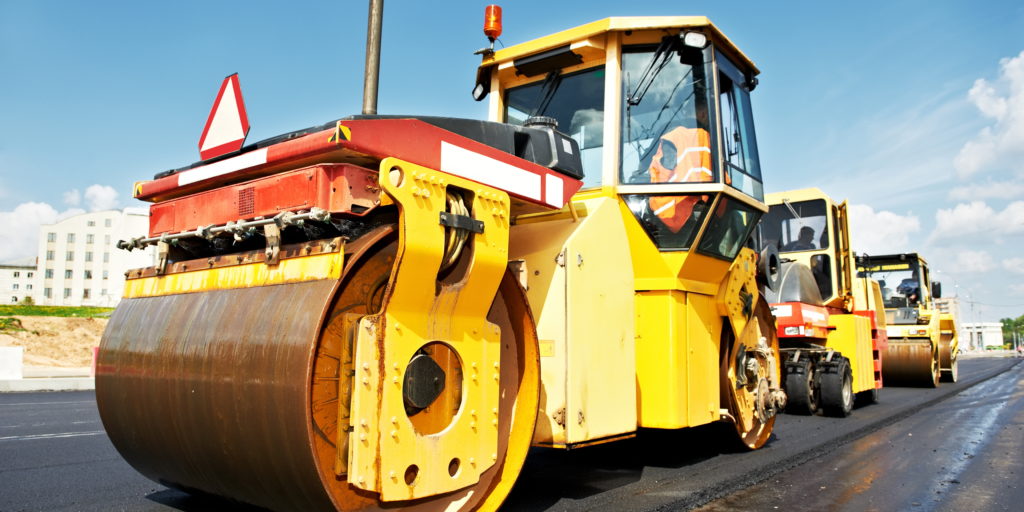
A paving machine spreads the mix of asphalt consistently with a consistent texture. Asphalt paving stones come in many shapes and sizes, allowing projects to be completed in various ways.
Other devices used in asphalt pavement installation include a roller or compactor for layer compaction, a dump truck for material delivery, and a milling machine for pavement removal.
Safety and Traffic Control
Asphalt paving should be constructed under the supervision of stringent safety and traffic control measures designed to protect workers and the general public. Asphalt paving contractors, like all construction workers, must observe the safety regulations and take measures to prevent accidents.
All personnel should wear personal protective equipment to prevent workplace hazards. You can also learn about hard helmets, HVVs, safety glasses, and steel-toed boots. Workers’ use of PPE frees them from falling objects and burning asphalt.
Traffic control is necessary for driver and pedestrian safety and to prevent pavement damage. Create a temporary traffic sign, barricade, or flagger to illuminate the area and keep it safe.
Consequently, the adequacy of preparation is one of the factors crucial for the long lifespan of asphalt pavement. For a paving project to be successful, proper site preparation, base material installation, subgrade inspection, drainage, asphalt mix design and testing, equipment and personnel requirements, along with safety precautions and traffic control, are needed.