Asphalt pavement, also referred to as asphalt concrete, is a widely used surface material in the construction of roads, parking lots, driveways, and other related areas. The process of putting asphalt pavement in place is complex, and, therefore, it must follow all the procedures expected in any construction project. These phases will be elaborated upon in detail in this article, from the initial steps of installation to completion.
Site Evaluation and Preparation
There are many steps involved in the installation of the asphalt surface, and the first is to assess the site and prepare it accordingly.
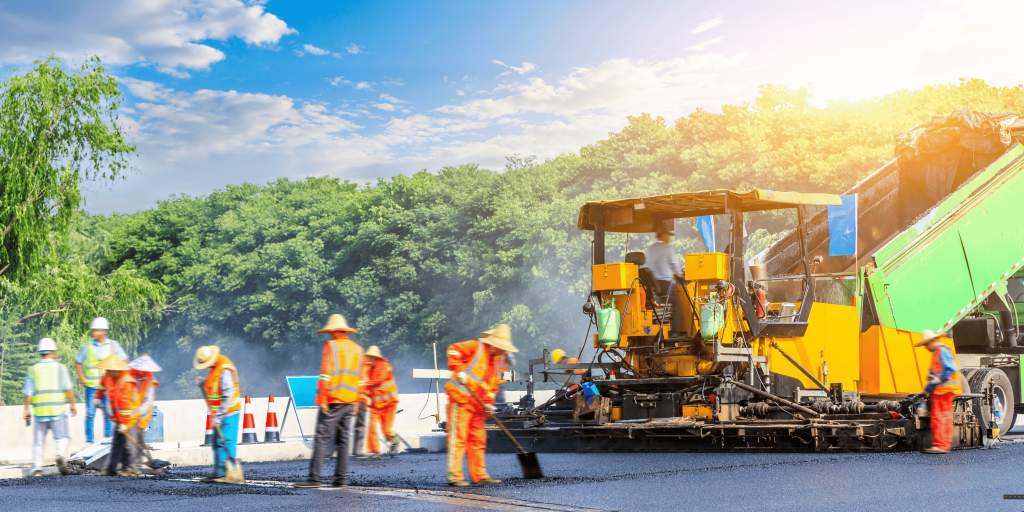
This involves:
– Measuring the area that needs to be paved and determining the amount of work that must be done and the materials to be used.
– Inspecting the substrate – this is the bottom layer of material upon which the asphalt will be placed, whether it is soil gravel or the current road base. It must be free from any large stones, even in size, and be well-leveled.
– Fixing any cracks, potholes, etc. for the base.
– Ensuring that there are curbs and gutters, drains, and any underground utilities that may not currently be in the area.
Once the base works are done, the subgrade, which is the ground beneath the base, must be compacted to hold the weight in the completed pavement. A steel drum roller is commonly used to comply with the subgrade to 95% density.
The Theoretical and Practical Aspects of Asphalt Mix Design and Production
The specific asphalt mix design must comply with the established transport agency specifications and project needs. The asphalt mix comprises aggregate as the main ingredient, crushed rock, and the asphalt binder, a sticky substance derived from petroleum. Using a blend of fine sand to coarse rocks, all proportions are appropriately combined, and hot asphalt cement is added to make the mix. This mixing is often done at an asphalt plant where the aggregate, filler, and binder are blended.
Tack Coat Application
When preparing the pavement for the placement of hot asphalt mix, a tack coat must be applied on the compacted base or the existing pavement surface. This thin layer of liquid asphalt simply acts as a means of ensuring that the new layer of asphalt covering is suitably anchored to the existing surface. The tack coat minimizes slippage and allows for proper water sealing. It is spread over the surface by a tack coat spray truck in such a manner that it forms a thin, uniform layer.
Asphalt Paving
When the site has been cleared and leveled, it is time to provide a base for the paving. The hot asphalt mix is transported to the site by dump trucks and tipped off into the paver hopper. The paving machine then directs and levels the mix to the required thickness or depth over the area. Workers must ensure adequate density and use care because it is dangerously hot (approximately 300 degrees Fahrenheit).
The two parameters of strength and durability of the compacted material are crucial for success. Several rounds of steel drum rollers pass over the asphalt again and again after the first layer has been laid by a heavy paving machine, and the temperature of asphalt is still high. This helps in the proper compaction of the material. Density testing can be conducted after compaction to determine the extent to which the specifications have been met.
Joint Construction
Where the new asphalt is being placed against the existing surface, a joint should be appropriately built, for instance, at the patch boundary. The existing pavement is cut vertically in a straight line that runs from one side to the other. The new asphalt is close enough to the edge of the old pavement, so it overlaps slightly. This is important because sealing the joint with a liquid asphalt emulsion seals off the area from water penetration. Correct procedures for constructing the joints ensure they do not crack or ravel.
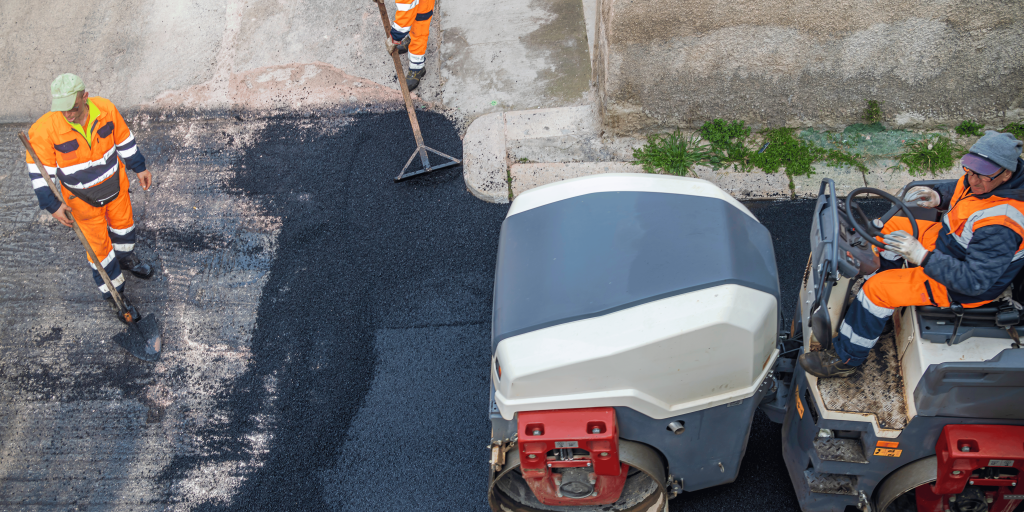
Grading, Compaction, & Minor Touches
Finally, after pavement construction, the asphalt’s top layers are grounded to achieve an appropriate drain slope and surface texture. Further drumming is carried out to compact the surface and edges, and the process is complete when the temperature is at its peak to get the maximum density. In the end, pavement markings, traffic signs, and other minor details that can be completed before the next phase are put in place to allow the roads to be opened for use.
Conclusion
Laying of asphalt pavement is an elaborate procedure involving various stages, including site work, materials and construction equipment, quality assurance, and project delivery to be successfully implemented. When constructed and built using the best quality materials, asphalt concrete pavements create long-wearing, smooth, low cost, and low-maintenance surfaces. Paying attention to detail in subgrade preparation and the last touch of markings means numerous years of paved surfaces.